AURIX TC3xx overview
The AURIX™ platform is a family of high-performance multi-core microcontrollers with multiple TriCore™ CPUs, program and data memories, interconnect and interconnect arbitration, interrupt system, DMA controller, and a powerful set of on-chip peripherals. The platform is designed to meet the requirements of the most demanding embedded control system applications where the competing aspects of price and performance, real-time responsiveness, computational power, data bandwidth, and power consumption are key design elements. It offers several versatile on-chip peripheral units such as serial controllers, timer units, and analog-to-digital converters.
The AURIX™ platform provides safe and secure real-time computing, and a scalable, dependable, and robust architecture. The enhanced TriCore™ 1.8 multi-core architecture comes with floating point units including double float support, and virtualization support. Further functional highlights are a dedicated real-time control sub-system, routing engines, and a proven ecosystem, including software and tooling.
In the AURIX ™ TC3xx product family, all peripheral units are connected to the TriCore™ CPUs and system through a flexible peripheral interconnect (FPI) and a shared resource interconnect (SRI). A number of IO (Input Output) lines on the TC3xx ports are reserved for these peripheral units to communicate with the outside world.
The TriCore™ processor architecture combines three powerful technologies within one processing unit, achieving new levels of power, speed, and economy for embedded applications. These are a reduced instruction set computing (RISC) processor architecture, digital signal processing (DSP) operations and addressing modes, and on-chip memories and peripherals.
The RISC load and store architecture provides high computational bandwidth with low system cost. DSP operations and addressing modes provide the computational power necessary to efficiently analyze complex real-world signals. On-chip memory and peripherals are designed to support even the most demanding high-bandwidth, real-time, embedded control system tasks.
Figure 1. AURIX™ TC37x block diagram
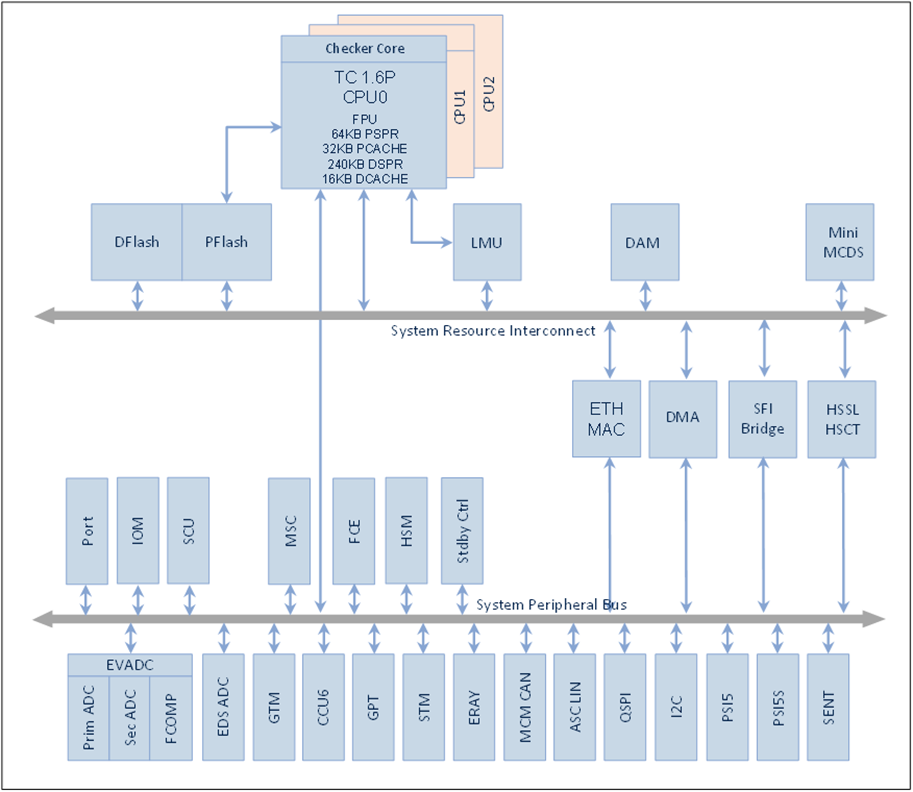
For information about the AURIX™ TC3xx portfolio, see Products.
Platform core target applications
The AURIX™ TriCore™ (TC) architecture is designed as a best in class product for automotive microcontroller applications. The microcontroller family includes various derivatives, which differ in their characteristics and functionality depending on the target application. For this brochure, we have selected the TC375 microcontroller as an example to illustrate the range of applications and functions. The system architecture is optimized to support the following core applications.
Powertrain engine control for multi-point injection (MPI), gasoline direct injection (GDI), diesel direct injection (DDI), and homogeneous charge compression injection (HCCI)
Powertrain transmission control, comprising continuously variable transmission (CVT), double clutch transmission (DCT), and automated manual transmission (AMT)
Powertrain for electric vehicles (xEV), addressing hybrid control unit (HCU), inverter, DC/DC converter, battery management systems (BMS), fuel cell, and on-board charger
Chassis and safety applications comprise braking, steering, suspension, and airbags
Advanced driver assistance systems (ADAS) address sensor data fusion and safety companion, as well as automotive radar sensors
Connectivity gateways provide services for telematics host control (interface to a cellular modem), gateway and domain control (in-car domain to domain), and zone control
System application use case
In addition to the core target applications there are features of the architecture that have been designed to support system use-case for a variety of applications. The example below shows a use case.
xEV: Automotive traction inverter
In electrified vehicle (EV) development manufacturers introduce electrified models to improve fuel economy and to remain competitive in a market where consumer demand shifts towards efficient, cleaner vehicles. These include hybrid electric vehicles (HEVs), plug-in hybrid electric vehicles (PHEVs), battery electric vehicles (BEVs), and fuel cell vehicles (FCVs). At the heart of all electrified powertrains is one or more electric machines (EMs) which either operate in conjunction with an internal combustion engine (ICE) or replace it entirely.
The traction E-Motor systems found in current EVs are most commonly of the AC permanent magnet (PM) or AC induction machine (IM) type. To drive them, a traction inverter is required to convert the direct current available from the battery pack to a variable frequency alternating current. In addition to the motoring mode the machines can also operate as generators, requiring the inverter to act as a rectifier and return energy to the battery.